Instandhaltung : Instandhaltung: IBS bringt Transparenz in Maschinenpark
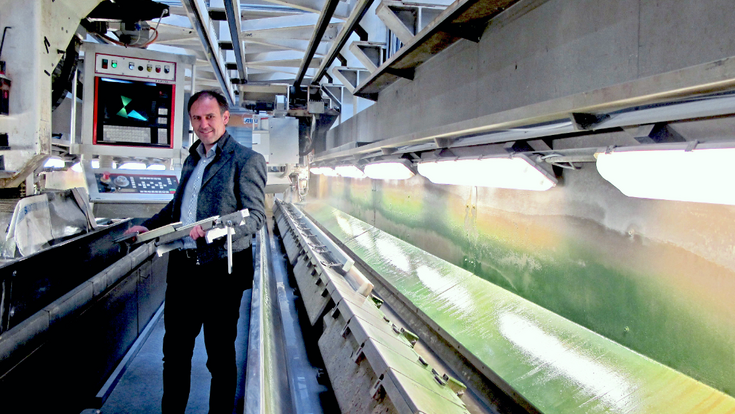
Das hat Einsparpotenzial. Eigentlich hatte Karl Knoflach den Auftrag die Instandhaltung auf ein Minimum zu reduzieren. Als nicht produktive Kostenstelle sei sie viel zu teuer, war der Tenor der Geschäftsleitung. Auf der Suche nach einer nachhaltigen Lösung entschied sich der Produktionsleiter mehr Transparenz in seine Fertigungsprozesse zu bringen. Im kleinen obersteirischen Teufenbach läuft seitdem eine Instandhaltungsstrategie, die nicht nur die Produktivität dieses Maschinenbauers um zwölf Prozent gesteigert hat, sondern dem Unternehmen IBS seitdem satte 60.000 Euro Instandhaltungskosten pro Jahr spart.
Die Grenzen der Zuständigkeit durchbrechen.
Wer in diesem Teil der Obersteiermark unterwegs ist, würde nie vermuten, dass sich in Teufenbach das Headquarter eines Weltkonzerns befindet. Weltweit bekannt unter dem Namen IBS Paper Performance Gruppe haben sich die Steirer in den letzten Jahrzehnten zu einem internationalen Top-Player der Papierindustrie gemausert. Ihre Spezialität: patentierte Technologielösungen für den Prozess der Papiererzeugung. Karl Knoflach leitet seit 15 Jahren die Produktion am Standort Teufenbach. Er kennt die Routine im Schichtbetrieb wie seine Westentasche. Im 3-Schicht-Betrieb fertigen die Mitarbeiter sechs unterschiedliche Produktgruppen als Zusatz für Papiermaschinen weltweit. Oberstes Ziel jedes Schichtführers dabei: „Die Produktivität der eignen Schicht möglichst hoch zu halten“, erklärt Knoflach. „Alles darüber hinaus verlässt die Grenzen der Zuständigkeit.“ Die Folge: Bei Übergabe an die darauffolgende Schicht waren unter anderem Werkzeuge verschlissen. Eine Verzögerungen und Verschwendung wertvoller Ressourcen. „Etwas das sich heute keiner mehr leisten kann“, so Knoflach. Es musste eine Lösung her. Der Produktionsleiter suchte nach einer Möglichkeit, wie er eine Top-Instandhaltung seines Maschinenparks für jede Schicht garantieren konnte. Seine Idee dabei: „Die Instandhaltung sowohl organisatorisch als auch systemtechnisch mit der Produktion zusammenzuführen.“
Effizienz – Visualisierung im Maschinenpark.
Eher zufällig traf er dann vor fünf Jahren bei einem gemeinsamen Kunden auf eben jenen Mann, der ihm das ermöglichen sollte. Johannes Stimpfl ist Geschäftsführer des Softwaresystemhauses Gamed und hat sich vor allem auf Instandhaltung- und Prozessoptimierung spezialisiert. Das Duo verstand sich auf Anhieb und legte damit den ersten Stein für eine langjährige Partnerschaft. Lange bevor ein Tool aus dem Hause Gamed zum Einsatz kam, galt es die Abläufe bei den Teufenbachern organisatorisch zu verbessern. „Ziel war es den Mitarbeitern an der Maschine gewisse Wartungsarbeiten zu übertragen“, erklärt Stimpfl. Was einfach klingt, ist psychologisch sehr schwierig. „Jemanden der viel zu tun hat, noch mehr geben, ist sehr heikel“, erinnert sich auch noch Knoflach an die damalige Stimmung am Shopfloor. Dennoch schaffte der Produktionsleiter ein Umdenken bei seinen Mitarbeiter. „Denn wer seine Maschine in einem Top-Zustand an die nächste Schicht übergibt , sorgt insgesamt für eine höhere Verfügbarkeit“, so Knoflach. Für eine bessere Dokumentation wurde im Folgeschritt die Instandhaltungsmanagementsoftware IPC installiert. Das Gamed-Tool unterstützt die Koordinierung und Abwicklung aller Wartungen, Inspektionen und Verbesserungen. „Damit bekamen wir erstmals mehr Transparenz in unseren Maschinenpark“, so Knoflach.
Leichtere Störungsanalyse.
Vor allem das standardisierte Erfassen von Störungen an der Maschine war für den Produktionsleiter das Non-Plus-Ultra. „Vorher hatte jeder seine eigene Art Fehler zu beschreiben“, erklärt Knoflach. Für jede Störanalyse hieß es sich in mühseliger Kleinarbeit zuerst durch drei bis vier Ordner Papierkram zu kämpfen. „Und selbst dann hatten wir nur oberflächliches Datenmaterial“, erinnert sich Knoflach noch gut. Mit dem IPC-Tool konnte nun jeder Fehler kategorisiert und mit einem Quotienten hinterlegt werden. „Jetzt hat jeder Mitarbeiter eine Auswahl an Fehlermöglichkeiten, die er dann rausfiltern und bewerten kann“, so Stimpfl.
Auch seine Lagerleichen ist Knoflach mit der Gamed-Lösung losgeworden. „Vor allem in Ersatzteillagern befinden sich oft Bestände, wofür es nicht mal mehr Maschinen gibt“, warnt Stimpfl vor unterschätzten Lagerkosten. Bei den Steirern wurde das Lager bedarfsbezogen optimiert und bindet seitdem viel weniger Kapital. Gamed entwickelte außerdem eine eigene Schnittstelle zum ERP-System im Betrieb. Das Personal der Instandhaltung hat somit jederzeit Einblick in die Bestände und kann bei Bedarf entsprechend disponieren. „Wer präventiv erkennt, wann eine Maschine Zicken macht, und zeitgleich Einblick in sein Lager hat, braucht keine Engpässe mehr zu fürchten“, so Stimpfl. Immerhin bis zu 10.000 Euro spart sich der Produktionsleiter seither pro Jahr an Lagerkosten.
Durch Visualisierung 60.000 Euro gespart.
Um vollste Transparenz in der Fertigung sowie Instandhaltung zu bekommen, wurde noch ein weiteres Tool, der OEE Analyser, installiert. Damit gelang es die operative Leistung der Instandhaltung darzustellen. Eine praktische Rarität, kennen Produktionen sonst nur die Kostenseite der Instandhaltung. „Das Tool liefert genauste Leistungsdaten der Maschinen sowie aufgetretene Fehler und Verluste in Echtzeit“, erklärt Stimpfl. Für IBS Austria ein ideales Cockpit für die Steuerung sämtlicher Abläufe. Stimpfl veranschaulicht das betriebswirtschaftlich. „Wenn der OEE-Analyser quasi die Aktiv-Seite der Instandhaltungsbilanz ist, dann wäre das IPC-System die strategische Passiva. Beide zusammen ergeben ein transparentes Instandhaltungscontrolling.“ Dass so ein Controlling auch gegenüber der Geschäftsführung Bestand hat, beweisen Knoflachs Zahlen. Satte 60.000 Euro pro Jahr sparen sich die Steirer seither an Instandhaltungskosten bei gleichzeitiger Produktivitätssteigerung von 12 Prozent. Zahlen, die jedem Geschäftsführer auf der Zunge zergehen. Damit war eines klar, an ein Outsourcing der Instandhaltung oder gar Reduktion war nicht mehr zu denken. Mit einem flexiblen Arbeitszeitmodell der rund 10 Instandhalter kann seitdem eine 24-Stunden-Verfügbarkeit garantiert werden. „Das bedeutet eine dramatische Änderung der Reaktionszeit, sollte tatsächlich mal etwas passieren“, so Knoflach.
Dank dieser Visualisierung in der Produktion und der damit verbundenen Instandhaltungsstrategie konnten in Teufenbach nicht nur die Durchlaufzeiten der Aufträge verkürzt, die stückbezogenen Fertigungskosten gesenkt sondern auch die Produktivität gesteigert werden. Ein Erfolg der dafür Sorge trägt, dass auch in Zukunft Weltkonzerne in der Steiermark wettbewerbsfähig produzieren können und damit Arbeitsplätze sichern.