Luftfahrt : Hightech-Prüfzelle für Hubschrauber am Wiener Getreidemarkt
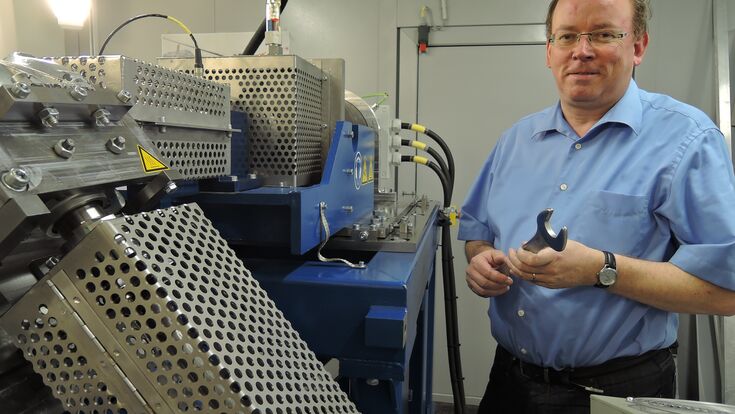
„Keiner will der Erste sein.“ Michael Weigand kennt die Sorgen der Hersteller von Hubschraubergetrieben. „Die luftrechtlichen Nachweisversuche über die Zuverlässigkeit bedeuten mehrere hundert Stunden Tests “, so der Institutsleiter für Konstruktionswissenschaften, Forschungsbereich Maschinenelemente an der TU Wien. Ein Prozess, der sich, laut Weigand, über Jahre ziehen kann. Optimierungswille stößt hier auf gesetzliche Zulassungen und beißt sich die Zähne aus. „Die Hersteller fliegen lieber mit bewährten und hundertprozent zuverlässigen Getrieben, als auch nur an einer Schraube zu drehen“, so Weigand. Technisches Optimierungspotenzial, das bewusst vergeudet werden würde, gäbe es da nicht das TU-Labor am Getreidemarkt in Wien. Nirgendwo sind die Auflagen strenger.
Es ist der Sicherheitsaspekt, der die Konstruktion von Luftfahrtantrieben so knifflig macht. „Alle Entwicklungen unterliegen strengen luftrechtlichen Vorgaben“, erklärt Weigand. Die sogenannten „Certification Specifications“ verlangen für den jeweiligen Luftfahrtzeugtyp sowohl die theoretischen Funktionsnachweise als auch die experimentellen Nachweise des Betriebsverhaltens. Ein enormer Aufwand für jeden Hersteller. Dem gegenüber stehen die hohen Anforderungen, denen Getriebe für Luftfahrtzeuge genügen müssen. Dazu gehören neben geringem Gewicht, hohen Drehzahlen, enormer Leistung und engen Bauraumforderungen unter anderem sehr hohe Anforderungen an die Ausfallsicherheit und sichere Notlaufeigenschaften. „Vor allem die Getriebe eines Hubschraubers sind aufgrund der Autorotationsfähigkeit von Drehflüglern für dessen sichere Funktion unabdingbar“, so Weigand. „Verliert ein Getriebe zum Beispiel Öl, muss trotzdem sichergestellt sein, dass der Pilot noch mindestens eine halbe Stunde zum sicheren Landen zur Verfügung hat.“ Das sei, laut Weigand, einer der Gründe für die umfangreichen Anforderungen der sogenannten Certification Specifications an diese Baugruppen. Anforderungen, die dem großen Wunsch nach zum Beispiel leichteren Modellen im Weg stehen. Das FFG-Projekt OHA! (Optimierte Hubschraubergetriebe made in Austria) soll das ändern. Es zeigt Optimierungsmöglichkeiten im Hinblick auf Gewicht, Leistung und Wirkungsgrad auf. Kurz gesagt: „Gibt es eine neue technische Lösung am Markt, beweisen wir, dass sich diese auch lohnt“, erklärt Weigand die neutrale Position der TU Wien. Schiebel und Pankl als Partner mit an Bord.
Als 2011 der Startschuss für das OHA! Projekt kam, galt es Geld in die Hand zu nehmen und sich starke Partner zu suchen. Heute kann Weigand eines der best ausgestatteten Prüflabors sein eigen nennen und sichert sich so einen Platz in der Austrian Aeronautics Industries Group und ist, immerhin neben Organisationen wie der NASA und dem DLR, Teil eines weltweiten Gremiums für luftfahrttechnische Forschung . Als Partner holte er sich den österreichischen Drohnenspezialist Schiebel mit an Bord. Der seit dem Ukraine-Einsatz auch für jeden Laien ein Begriff sein dürfte. Auch Pankl Aerospace als renommierter Hersteller vor allem von Antriebswellen und Getrieben für Hubschrauber ist am OHA!-Projekt beteiligt und liefert die entsprechenden Antriebswellen. „Bei uns werden alle Getriebecomponenten des „camcopters“ von Schiebel, aber auch von Kleingetrieben bemannter Hubschrauber in Hinblick auf ihr Verbesserungspotential evaluiert. Tribologische Aspekte spielen hier einen besonderen Schwerpunkt“, erklärt Weigand. Das große Ziel: Die Getriebe des camcopters zu optimieren, und weiters im Anschluss auch luftrechtlich zu qualifizieren werden können. Immerhin 20 mal 7 Meter misst die dafür erbaute modulare Prüfzelle am Getreidemarkt. Bei Versuchsablauf herrscht strenges „Betreten verboten“. „Harmlose Schrauben können bei einer Geschwindigkeit von mehr als 7.000 Umdrehung pro Minute zu echten Geschossen werden“, warnt Weigand. Viel zu gefährlich also, um selbst das Getriebe zu beobachten. Diesen Einsatz übernimmt ein praktischer Helfer: eine Wärmebildkamera. Testo gewinnt das Herstellerrennen.
Das Herstellerrennen war hart, denn die Anforderungen der TU-Spezialisten waren groß, dennoch sollte die Kamera in einem gewissen Budgetrahmen bleiben. „Gar nicht so einfach“, wie Weigand heute zugibt. Fündig wurde der Institutsleiter dennoch. Seit Beginn der Versuche ist das Modell 890-2 von Testo mit an Bord. Leicht und äußerst handlich liefert die Wärmebildkamera alle relevanten Daten in Echtzeit. Übertragen durch ein USB-Kabel können alle Temperaturverläufe nachverfolgt und auch im Nachhinein beliebig oft aufgerufen werden“, erklärt der Professor. Factory konnte sich live vor Ort überzeugen und den anfangs doch unscheinbaren Thermomeister bei der Arbeit zu sehen. So konnte an einem Prüfstand genau nachverfolgt werden, wie stark sich das Getriebe erhitzt. Die technischen Hintergründe dazu liefert Weigand: „Je nachdem, welches Öl wir nehmen, sehen wir, ob mehr oder weniger Kraft übertragen werden kann.“ Ende des Jahres wird das OHA!-Projekt seinen Abschluss finden. Geht es aber um die Endergebnisse lässt Michael Weigand die Öffentlichkeit noch zappeln. Nur soviel: „Wir konnten von einem neutralen Standpunkt aus beweisen, das es einiges an Optimierungspotenzial gibt.“ Eine unbefriedigende Aussage, dürstet den Leser doch nach Details. Aber ein Professor, der in seiner vorherigen Position als Konstruktionschef bei der Zahnradfabrik (ZF) in Friedrichshafen einem Hubschrauber einfach so 75 Kilogramm mehr Nutzlast verschaffte, ist mit Sicherheit auch ein Durchbruch in Wien zuzutrauen. „Und bis Ende des Jahres sind es ja nur mehr vier Monate“, bemerkt der Institutsleiter mit einem Lächeln im Gesicht.