Forschung : Transformers: Ein EU-Projekt soll den LKW zum Spritsparwunder machen
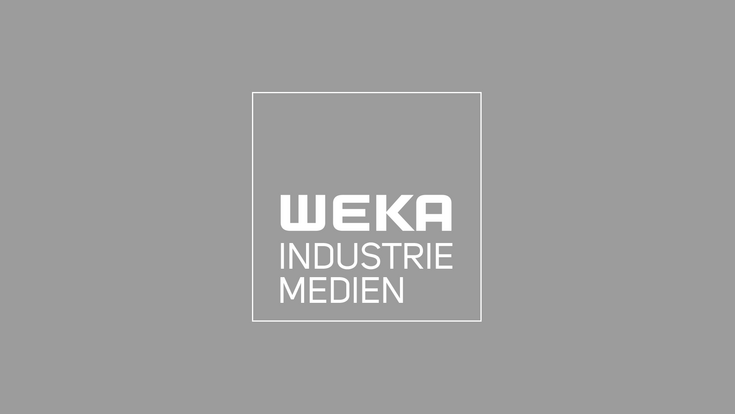
Das Gros der Güter wird europaweit, weltweit mit Lkw vom Hersteller zum Konsumenten transportiert. Der Lkw gilt als flexibel, aber der Ruf nach mehr Effizienz steht seit längerem im Raum. Im EU-Forschungsprojekt Transformers (Configurable and Adaptable Trucks and Trailers for Optimal Transport) hat ein internationales Konsortium zwei Lösungen erarbeitet, wie der Gütertransport mit Lkw künftig kostengünstiger und effizienter werden könnte.
Transformer-Trailer brauchen weniger Sprit
Gelingen soll das mit einem Hybridantrieb im Lkw, Anpassung der Anhängerarchitektur und mehr Aerodynamik beim Design des Lkw. Bekannte Firmen wie die Lkw-Hersteller Volvo und DAF, Schmitz Cargobull und TNO und Van Eck sowie Forschungseinrichtungen wie TNO, Virtual Vehicle, Ifstar und das Fraunhofer-Institut für Betriebsfestigkeit und Systemzuverlässigkeit (LBF) in Darmstadt waren bei diesem von der EU geförderten Projekt mit von der Partie. Das LBF hat dabei eine Sensorik zur Ladevolumenmessung sowie ein Batteriegehäuse zur Versorgung eines elektrischen Hilfsantriebes im Trailer entwickelt. „Die Transformers-Trailer verbrauchen bis zu 25 Prozent weniger Kraftstoff, insbesondere beim Transport von palettierten Waren“, erklärt Thorsten Koch, Projektleiter beim LBF gegenüber Factory.
EU sieht das Projekt als Erfolg
Die Treibstoffeinsparung steht im Vordergrund, weil diese einen am meisten fassbaren und nachvollziehbaren Wert darstellt. Erreicht wird dies durch die anwendungsspezifische Anpassung der Lkw-Struktur, einen im Auflieger (Lkw-Anhänger) verbauten elektrischen Hilfsantrieb, eine anpassbare Beladungskapazität sowie eine ganzheitlich optimierte Aerodynamik. Für die Lkw-Fuhrparkbetreiber verringern sich die Kraftstoffkosten pro Tonnen-Kilometer, der CO2-Ausstoß sinkt, und die Staugefahr an Steigungen und im Stadtverkehr nimmt ab, so einige der Ergebnisse bei diesem Projekt, das erst kürzlich von der EU als „Success Story“ eingestuft wurde.
Modularer Ansatz für Beladung
Lkw sind derzeit in erster Linie für ein maximales Ladegewicht ausgelegt. Das Projekt Transformers setzt dagegen mit dem Load-Optimization-Trailer und dem Hybrid-on-Demand-Trailer (HoD) auf einen modularen Ansatz, der die Lkw für die Beladung anpasst. Dabei kommt es auf modulare, hybride Antriebskonzepte einschließlich aerodynamisch und beladungsoptimal angepasster Fahrzeugarchitektur an. In der Praxis heißt das: Die Frontseite des Lkw-Anhängers/Trailers bekommt ein aerodynamisches Design, das Dach wird aerodynamisch abgesenkt. Im Inneren braucht es ein speziell konstruiertes Batteriegehäuse sowie einen Ladevolumensensor. Der sogenannte Load-Optimization-Trailer des Anhänger-Herstellers Van Eck verfügt über eine elektrische Dachhöhenverstellung, einen Ladevolumensensor und ein Double-Floor-System. Ist beispielsweise die zulässige Gesamtmasse des Aufliegers erreicht, ohne dass sein Volumen voll ausgenutzt wird, so lässt sich das Dach absenken, um den Luftwiderstand zu reduzieren. Die jeweils aktuelle Ausnutzung des Ladevolumens ermittelt das vom Fraunhofer LBF entwickelte Sensorsystem zur Messung der Ladungshöhe. Ist die zulässige Gesamtmasse hingegen noch nicht erreicht, können mit Hilfe des Double-Floor-Systems auf Paletten verstaute Waren übereinander verladen werden, um die maximale Ladungshöhe voll auszunutzen und damit die Transporteffizienz zu erhöhen.
Schmitz Cargobull gewinnt Bremsenergie zurück
Der HoD-Trailer von Schmitz Cargobull verfügt über eine manuelle Dachhöhenverstellung und einen Hybrid-on-Demand Antrieb mit Energierückgewinnung. Ähnlich wie beim Load-Optimization-Trailer lässt sich die Dachhöhe des Trailers an die tatsächliche Ladungshöhe anpassen um den Luftwiderstand zu reduzieren. Als sogenanntes HoD-System sorgt der im Auflieger installierte elektrische Antriebsstrang für kurzfristig verfügbare Zusatzleistung, beispielweise für das Überwinden von Steigungen oder beim Anfahren. Genauso kann auf Gefällstrecken verlorene Bremsenergie zurückgewonnen werden. Die Batterie mit der dazu gehörenden Leistungselektronik sowie dem notwendigen Kühlsystem muss im Fahrbetrieb sicher am Unterboden des Aufliegers befestigt sein und im harten Alltagseinsatz vor den Einwirkungen der Umgebungsbedingungen wie etwa Steinschlag geschützt werden. Das dazu notwendige robuste Gehäuse ist am Fraunhofer LBF konstruiert und ausgelegt worden. Für eine zuverlässige Energieversorgung des elektrischen Hilfsantriebes im Trailer müssen das Batteriemanagementsystem und die Batteriezellen hohen Ansprüchen genügen. Daher sind sie gekapselt. Mit dem Transformers-Lkw wurde die ersten Hürden genommen, doch weitere stehen noch bevor, weiß Koch. Diese sollen im Nachfolgeprojekt Aeroflex überwunden werden.