Eberle setzt auf Zwilling von digifai : Schritt für Schritt: Eine Machbarkeitsstudie im Sondermaschinenbau
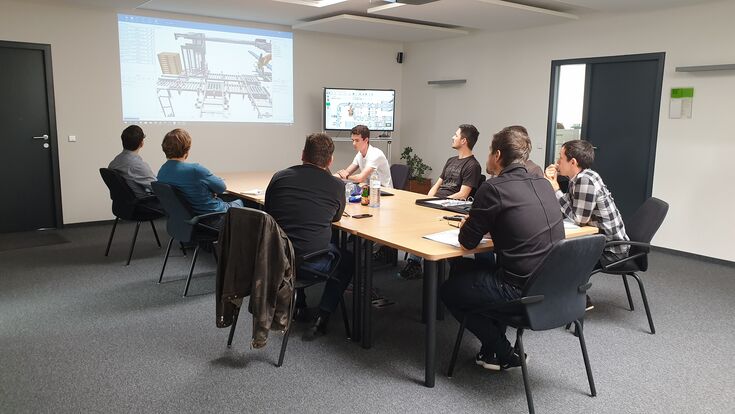
Eine Machbarkeitsstudie läuft in mehreren Schritten ab. Zu Beginn testet der Vertrieb verschiedene Problemstellungen mit dem Kunden. Im folgenden Schritt wird die Anlage virtuell im Detail konstruiert. Hier fügte man die zu fertigenden Produkte ein, testet etwa Taktzeiten und Roboterpositionen.
- © Eberle Automatische SystemeEine solche Machbarkeitsstudie läuft in mehreren Schritten ab. Zu Beginn testet der Vertrieb verschiedene Problemstellungen mit dem Kunden, z.B. welche Roboter, Förderbänder oder Paletten optimal wären und wie die Anlage aussehen müsste, um konsistent zu sein. Im folgenden Schritt wird die Anlage virtuell im Detail konstruiert. Hier fügte man die zu fertigenden Produkte ein, testet etwa Taktzeiten und Roboterpositionen. "Viele sind stolz auf ihre Erfahrungswerte, aber das reicht hier nicht aus. Man benötigt auch die von simulierten, denn die sind sicherer, außerdem testbar und man kann deshalb die Risiken rausnehmen", so Eberle-CEO Martin Moosmann. "Außerdem sind wir im Sondermaschinenbau tätig, da sieht jede Maschine anders aus und hat andere Probleme. Es gibt also kaum echte nutzbare Vergleichswerte."
Lesetipp: Know-how für die französische Raumfahrt aus Linz
Mit twin sieht der Kunde schon früh die Anlage mit ihren Ausmaßen und Funktionen, kann sie virtuell in seiner Produktionsumgebung aufstellen und ermitteln ob und wie er die innerbetriebliche Infrastruktur anpassen muss. Dazu können hier auch Bediener geschult werden und man sieht, ob die Funktionen vom Mitarbeiter gut handelbar sind und wie effizient sich im Notfall Wartungsarbeiten durchführen lassen.
Danach wird die Steuerungssoftware programmiert und getestet: Ist die Sensorik komplett oder hat man etwas vergessen? Über das Testen der realen Steuerung lassen sich der Anlage so mögliche Kinderkrankheiten schon vor dem Anlaufen austreiben. Das verursacht weniger Inbetriebnahmeschäden und damit Kosten. Ein weiterer Mehrwert ist, dass twin die ganze Anlage visualisiert und den hier erzeugten digitalen Zwilling in das in 3D-HMI spiegelt. Über diese Schnittstelle lässt sich eine optimale Fernwartung mit Fehleranalyse durchführen und der Bediener ist notfalls schnell in der Lage Fehler zu beheben.
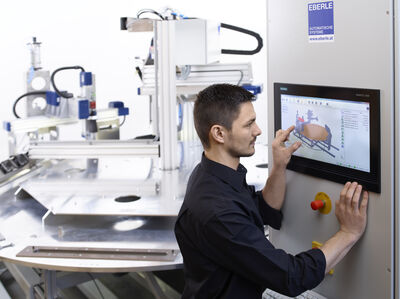
Intuitiv in einer neuen Dimension entwickeln
Bisher erstellt ein Programmierer ein provisorisches Steuerungsprogramm parallel zum Herstellungsprozess der Maschine, das im Vorfeld nur rudimentär getestet werden kann. Ganzheitliches Testen des Zusammenspiels aller Steuerungsebenen, Maschinenbereiche etc. muss unter Zeitdruck später an der realen Maschine beim Kunden durchgeführt werden. Da nicht alle Szenarien vollständig und vor allem im Dauerbetrieb getestet werden können, kann dies kostspielige Serviceeinsätze erzwingen, während denen die Produktion steht. Abhilfe schafft hier die Software twin. Sie begleitet den Anlagenbau von den ersten Entwicklungsansätzen bis zum Alltagseinsatz. Während der Designphase entwickeln die Ingenieure SPS-Programme am Modell und testen sie. So findet man früh mögliche Kollisionspunkte von Maschinenkomponenten und Werkstücken für ein verbessertes Anlagenkonzept.
Konzepte und SPS-Software am digitalen Zwilling testen
In der nächsten Phase, wird die Maschine anhand der konstruierten 3D-CAD-Daten als digitaler Zwilling nachgebildet. Um die Steuerungssoftware zu schreiben und zu testen, bindet man die virtuelle Maschine an die notwendigen Steuerungen an. Die digital gespiegelte Maschine besitzt die gleiche Aktorik und Sensorik wie das reale Pendant. Die angebundenen Steuerungssysteme sehen hier keinen Unterschied zur realen Maschine.
So lässt sich mit twin die neue Anlage vollständig in Echtzeit simulieren, mit allen Abläufen bei möglicherweise unterschiedlichen Taktzeiten von Maschinen und Logistikeinrichtungen. Hat der Kunde dann noch weitere Funktionswünsche, dann können diese fortlaufend integriert und getestet werden.
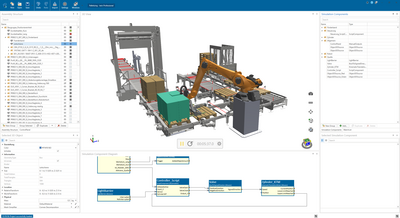
Vorteil der virtuellen Inbetriebnahme
Die Möglichkeit der virtuellen Inbetriebnahme macht den Entwicklungsprozess unabhängig von der Hardware. So können die Maschinenbauer schon, parallel zum Bau der Anlage Abläufe testen und notwendige Änderungen einbauen. Das bringt Sicherheit in den kompletten Entwicklungszyklus der Maschine. Außerdem können die späteren Bediener schon am simulierten Modell eingewiesen werden und üben. Treten dabei fundamentale Probleme bei der Bedienung auf, dann können die in dieser frühen Phase gelöst und die Maschine entsprechend angepasst werden. Das macht die Inbetriebnahme deutlich kostengünstiger und effizienter. Dazu kommt die Software bereits fehlerfrei auf die Anlage. Wenn überhaupt, sind dann die nötige Umbauphasen vor Ort kürzer und stören die Produktion weniger. Um wieviel twin den Entwicklungsprozess gegenüber konventionellen Verfahren verkürzt hängt dabei von der jeweiligen Anwendung ab.
Lesetipp: Lottmann lässt Waschtische von Roboter polieren
Und twin bietet weitere Vorteile. Bei der Fertigung neuer Produkte muss eine bestehende Anlage aufwändig adaptiert werden. Mit twin nimmt man die Änderungen am 3D-Modell vor und testet sie hier. Damit geht man sicher, das die adaptierte Maschine schnell den Betrieb aufnehmen kann – im Sinne einer flexiblen Produktion, wie für Industrie 4.0 nötig. Deshalb ist twin auch bei einem anstehenden Retrofit hilfreich. So lassen sich die Modelle bestehender Maschinenmodule übernehmen und virtuell mit den neuen verbinden und anpassen, was deutlich Kosten und Zeit spart. So spart twin mit dem digitalen Zwilling und dem 3D-HMI über die ganze Lebenszeit einer Anlage Kosten und ist somit eine Investition in die Zukunft.
Effizienter Maschinenbau
Mit twin kann man ausprobieren welche Aktoren und Sensoren man wirklich braucht und wie man Geschwindigkeiten, Taktzeiten, etc. aufeinander abstimmt für eine kosteneffiziente Fertigung, ohne teure Versuchsaufbauten. Außerdem lassen sich Verläufe simulieren, die im Maschinenalltag selten auftreten und so die Sicherheit der Anlange optimieren.
Auch im Marketing und Vertrieb leistet twin wertvolle Dienste. Der Kunde sieht die Anlage als realitätsgetreuen Animation, statt in 2D auf Papier. Das stellt sicher, dass keine Missverständnisse aufkommen. "Zudem verlagert sich die Zeit der Inbetriebnahme beim Kunden ins Engineering, was große Kosteneinsparungen mit sich bringt“, so Martin Moosmann. Die Software twin wurde von Eberle Automatische Systeme in enger Zusammenarbeit mit Personen aus der Praxis entwickelt. Das spiegelt sich in der Einfachen Bedienung wider.
twin bleibt als 3D-Visualisierung auf der Kundenmaschine und das ist eine echte Investition in die Zukunft, denn nicht nur Produkte ändern sich, es kommen auch neue Fertigungstechnologien dazu und der Unternehmer kann mit twin seine Steuerung stetig an die neuen Gegebenheiten adaptieren. Über twin und den damit verbundenen digitalen Zwilling, kann die Anlagentechnik stetig optimiert und an die aktuelle Technologie angepasst werden. Auch ein Retrofit bestehender Anlagentechnik lässt sich effizient durchführen. "Somit ist twin eine echte Investition in die Zukunft, denn mittels neuer Module kann die Software ergänzt werden, auch wenn Technologien kommen, die man heute noch nicht kennt", freut sich Martin Moosmann.